Production process of PET plastic roll
The Puster PET plastic roll production line adopts advanced extrusion-cooling-stretching process. The production process can be roughly divided into the following steps:
1. Raw material preparation: Mix and dry PET particles, masterbatch, additives and other raw materials.
2. Melt extrusion: The mixed raw materials are fed into the extruder and melted into PET melt under high temperature and high pressure.
3. Filtration and purification: Filter the PET melt to remove impurities and gases.
4. Flat film forming: The PET melt is cast into a thin film PET plastic roll through a mold.
5. Cooling and shaping: The PET plastic roll is cooled and shaped by a cooling roller.
6. Stretching: The PET plastic roll is biaxially stretched to improve its mechanical strength and transparency.
7. Cutting and finishing: The PET plastic roll is cut and finished according to specifications to make a finished product.
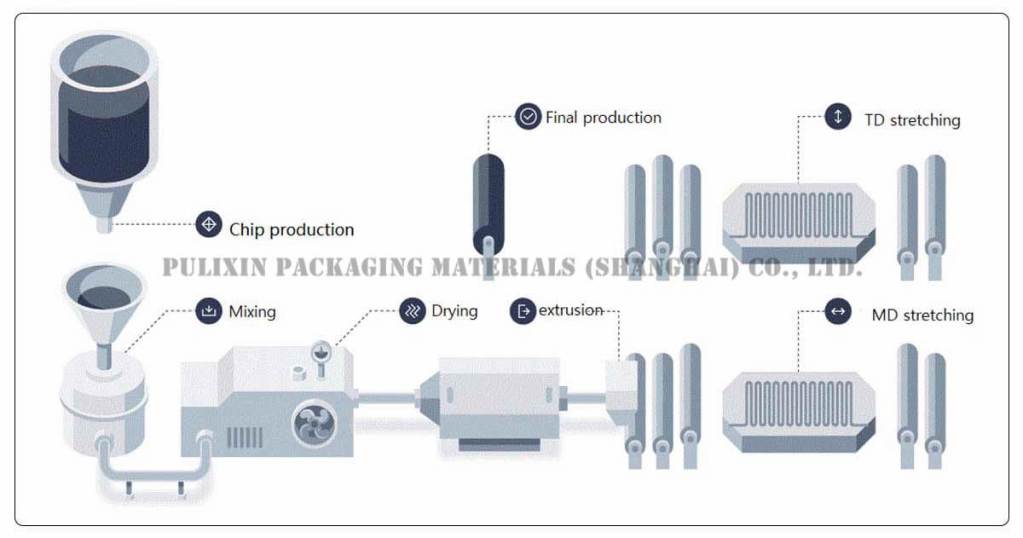
Production of colored PET plastic rolls
The production of colored PET plastic rolls is basically the same as that of transparent PET plastic rolls, but there is an additional step of adding masterbatch. In the raw material preparation stage, in addition to raw materials such as PET resin and additives, masterbatch needs to be added. Masterbatch is an additive composed of pigments, carriers, dispersants, etc., which can give color to plastic products.
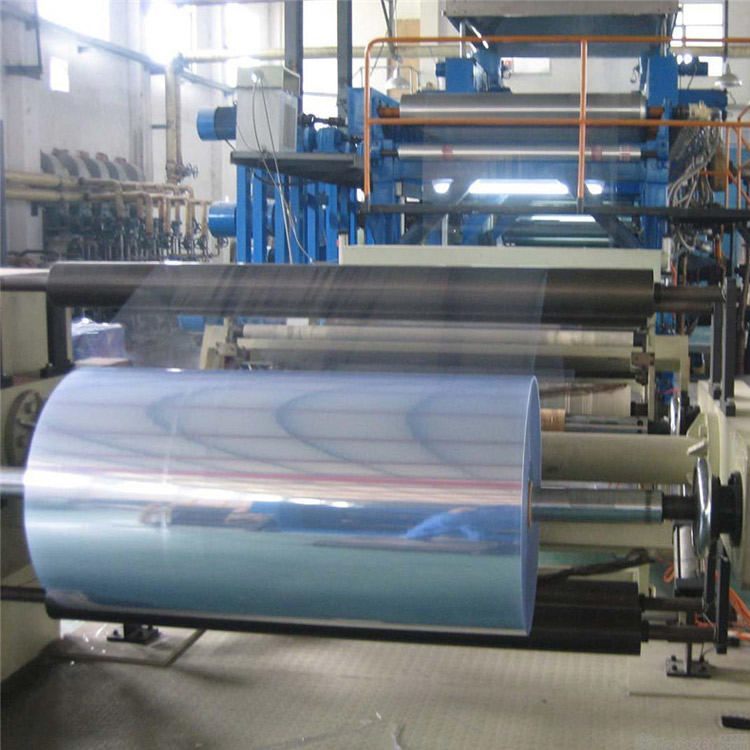
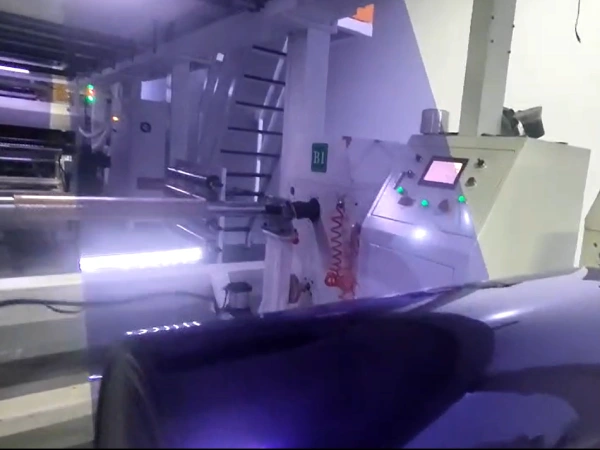
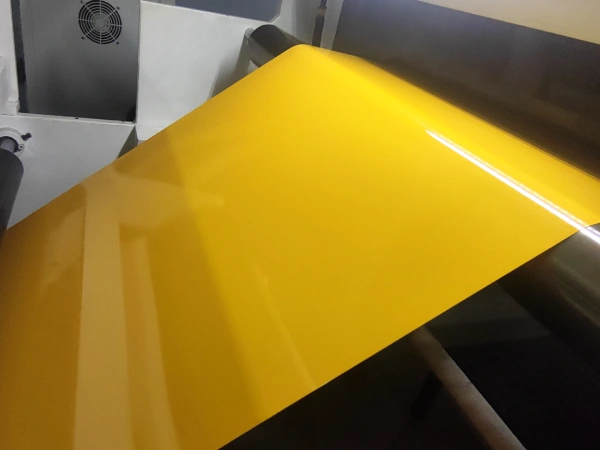
The difference between colored PET plastic rolls and transparent PET plastic rolls
Color: Colored PET plastic rolls have color, while transparent PET plastic rolls are colorless.
Transmittance: The transmittance of colored PET plastic roll is lower than that of transparent PET plastic rolls. The transmittance of colored PET plastic rolls depends on the amount and dispersion of pigments. The greater the amount of pigment, the lower the dispersion and the lower the transmittance.
Application: Colored PET plastic rolls are often used to make food packaging boxes, beverage bottles, cosmetic bottles, toys, etc., because the color can attract consumers' attention and improve the visual effect of the product. Transparent PET plastic rolls are often used to make food packaging boxes, beverage bottles, electronic product shells, etc., because transparency can show the appearance of the product and improve the grade of the product.
Comparison between colored PET plastic rolls and transparent PET plastic rolls
Characteristics | Colored PET plastic rolls | Transparent PET plastic rolls |
Color | Yes | No |
Transmittance | Low | High |
Applications | Food packaging, beverage bottles, cosmetic bottles, toys, etc. | Food packaging, beverage bottles, electronic product shells, etc. |
Advantages | Attract consumer attention and improve product visual effects | Show product appearance and improve product grade |
Disadvantages | Low transmittance | Easy to scratch |
Factors affecting the transmittance of colored PET plastic rolls
The transmittance of colored PET plastic rolls is influenced by several factors, ranging from the intrinsic properties of the PET material to the manufacturing processes and additives used. Here are the key factors affecting the transmittance:
1. Intrinsic Properties of PET
Polymer Quality: The purity and molecular structure of the PET polymer affect its optical clarity and, consequently, its transmittance.
2. Colorants and Additives:
Type and Concentration of Dyes/Pigments: The nature (organic or inorganic) and concentration of colorants significantly affect light absorption and scattering. Higher concentrations typically result in lower transmittance.
Additives: Other additives like UV stabilizers, optical brighteners, and processing aids can also impact the transmittance.
3. Manufacturing Process
Extrusion Conditions: The temperature, pressure, and cooling rate during extrusion can influence the crystallinity and optical properties of PET.
Thickness of the Film: Thicker films tend to have lower transmittance due to the increased path length for light absorption and scattering.
Quenching Rate: The rate at which the PET plastic roll is cooled affects its crystallinity. Faster cooling generally results in lower crystallinity and higher transmittance.
4. Physical Properties
Crystallinity: Higher crystallinity in PET reduces its transmittance because crystalline regions scatter light more effectively than amorphous regions.
Surface Finish: The smoothness and uniformity of the PET film surface can affect its optical clarity. Rough or textured surfaces scatter light, reducing transmittance.
5. Environmental Factors
Exposure to UV Light: Prolonged exposure to UV light can cause yellowing or other changes in the PET material, reducing its transmittance over time.
Temperature and Humidity: Variations in temperature and humidity during storage and use can affect the physical and optical properties of PET.
6. Contaminants and Impurities
Inclusions and Impurities: Any contaminants or impurities in the PET material can scatter light and reduce transmittance.
Dust and Particles: Surface contamination with dust or other particles can impact the optical clarity of the PET plastic rolls.
Pusite Manufacturer introduction of PET plastic rolls
Pusite has several significant advantages in the production of PET plastic rolls:
1. Advanced technology
Pusite uses advanced production equipment and process technologies to ensure high efficiency and high precision in the production process. These technologies include efficient extrusion and cooling systems, as well as automated quality inspection equipment to ensure that the quality of each roll of PET plastic meets the standards.
2. High-quality raw materials
Pusite strictly selects and purchases high-purity raw materials (such as terephthalic acid and ethylene glycol) to ensure the quality of the final product. High-quality raw materials can improve the transparency, strength and durability of PET plastic rolls.
3. Rich experience and expertise
Pusite has many years of experience in the field of plastic manufacturing and has accumulated rich expertise and skills. Their team includes experienced engineers and technicians who can effectively solve various problems in the production process and continuously improve the process.
4. Environmentally friendly
Pusite is committed to sustainable development and adopts environmentally friendly production processes and materials. PET itself is a recyclable material. Pusite minimizes waste and energy consumption in the production process and actively promotes the circular economy.
5. Diversified product lines
Pusite provides PET plastic rolls in a variety of specifications and colors to meet the needs of different customers. They are able to customize products according to customers' specific requirements, including thickness, width, color and functional additives, etc.
6. Strict quality control
Pusite implements a strict quality control system. From raw material procurement to final product delivery, every link is strictly tested and monitored to ensure that the products meet international quality standards such as ISO and FDA.
7. Excellent customer service
Pusite attaches importance to customer experience, provides professional pre-sales and after-sales services, can quickly respond to customer needs and feedback, provide technical support and solutions, and help customers solve practical problems.
8. Cost-effectiveness
By optimizing production processes and large-scale production, Pusite can effectively reduce production costs and provide customers with competitive prices.
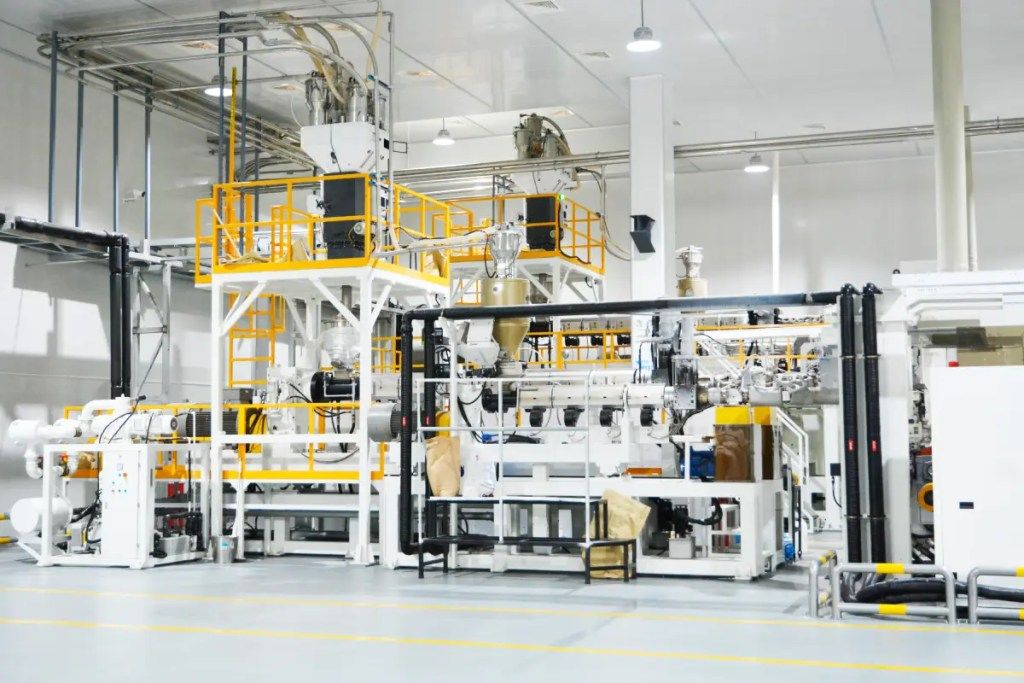
More products
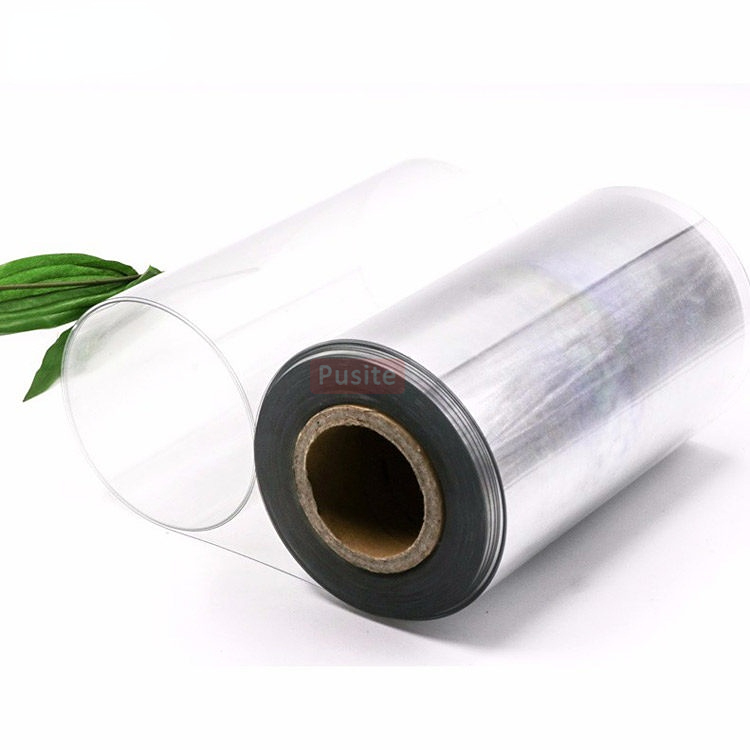
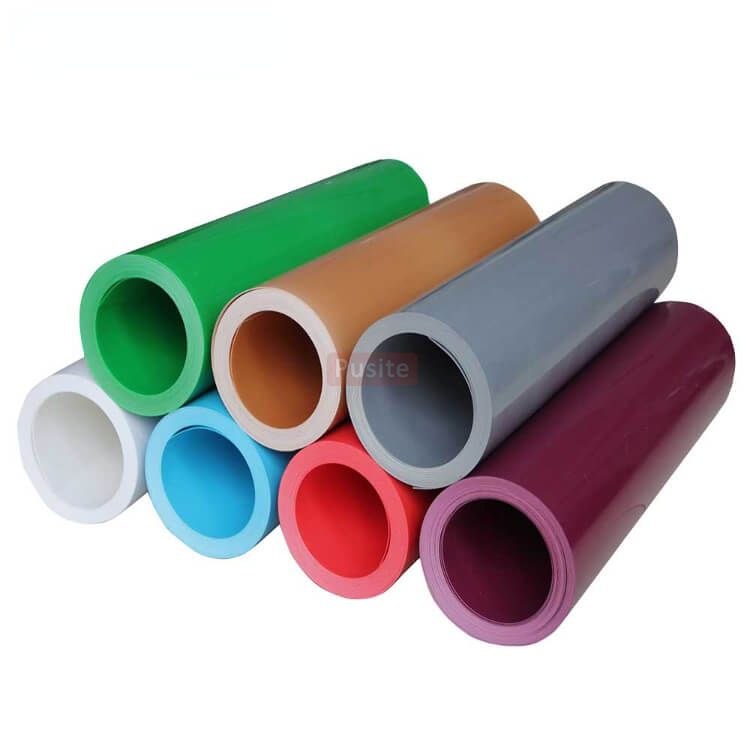
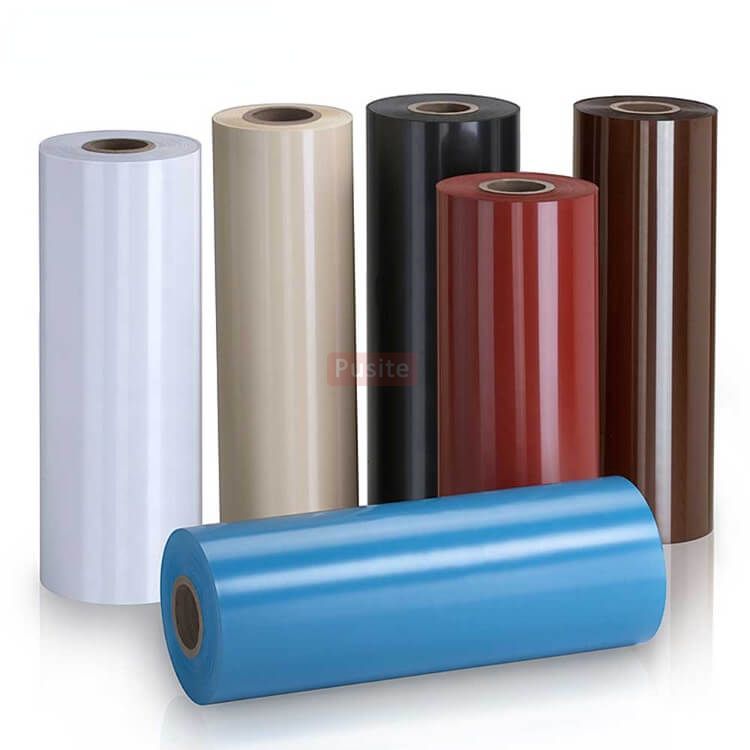
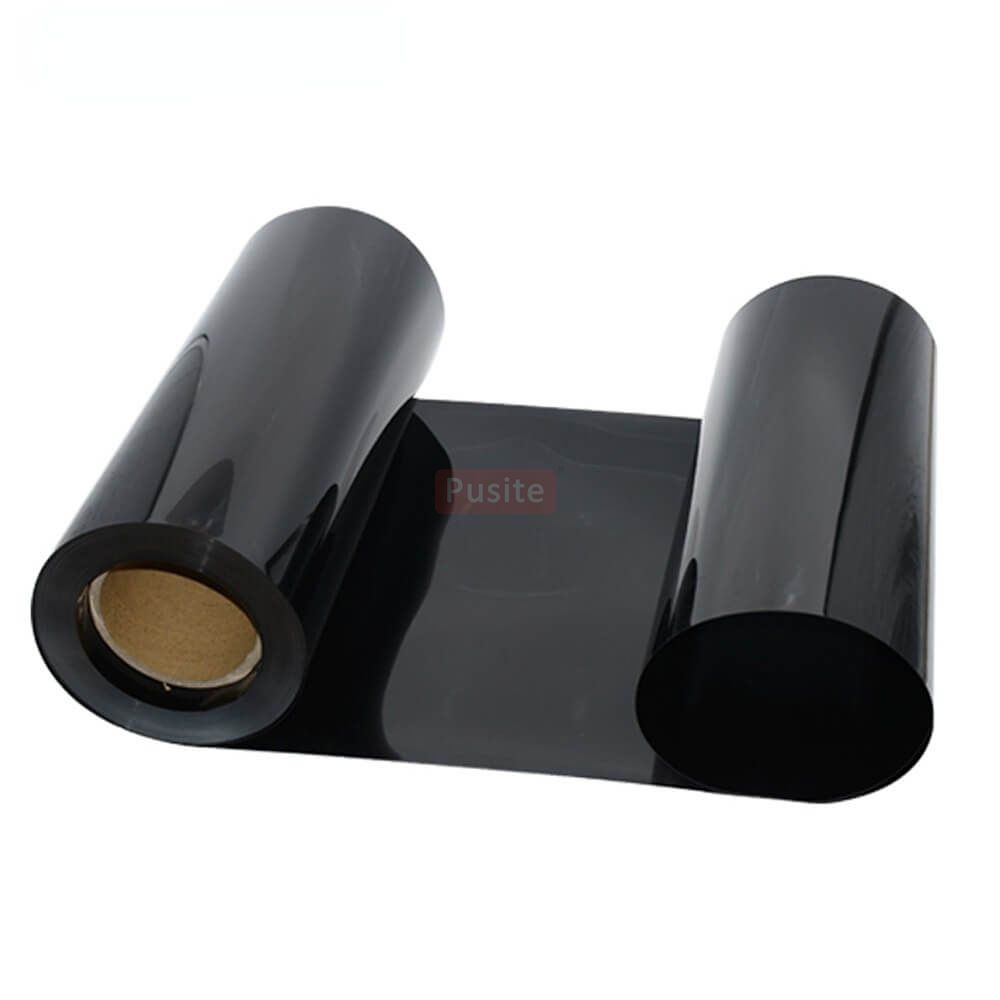
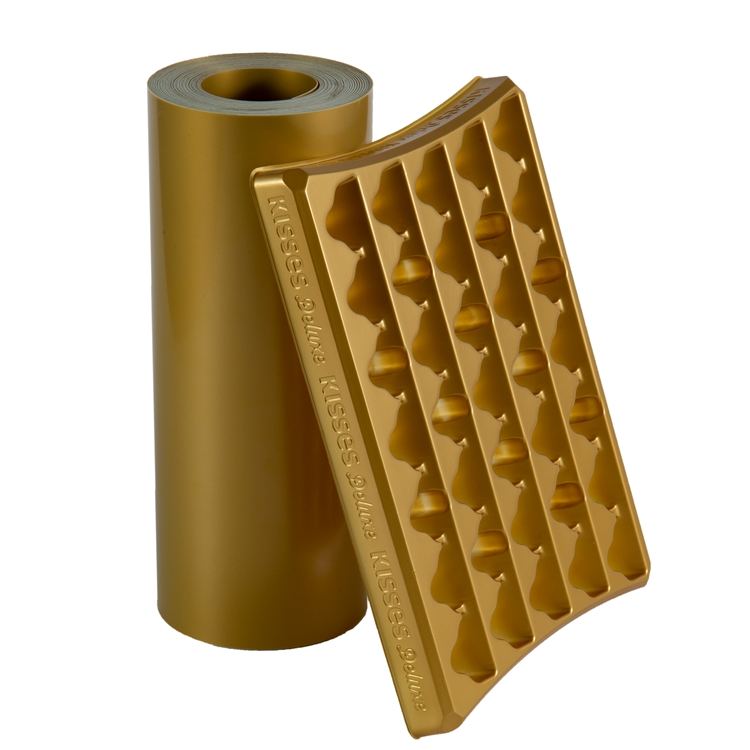
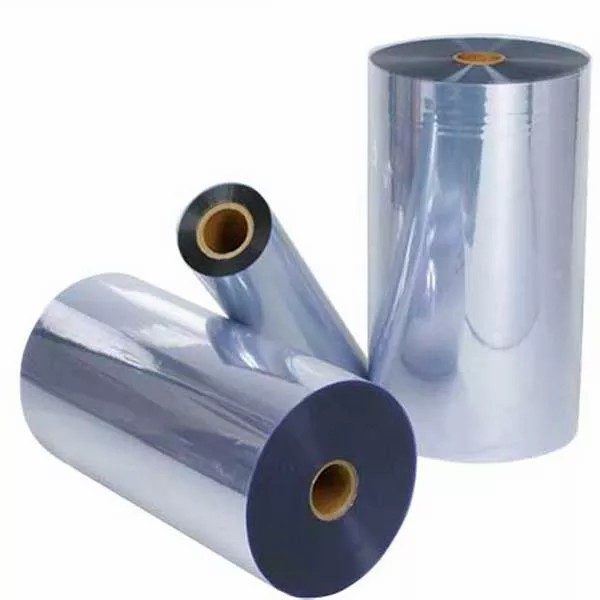