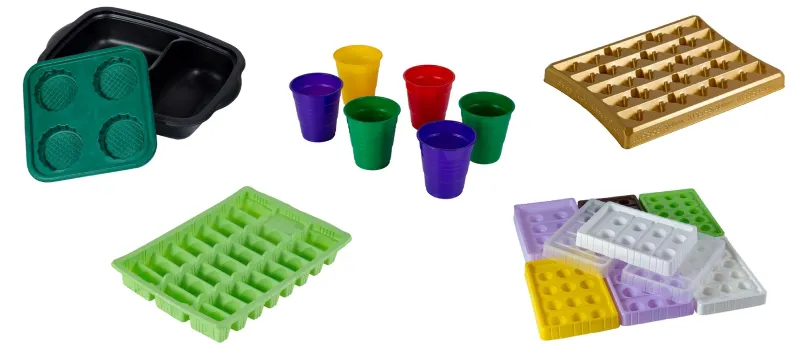
Advantages of blister packaging:
1. Blister packaging has strong plasticity and protection functions. The basic function of blister packaging is to protect products, especially during transportation, to avoid collisions between goods. Blister-wrapped custom grills can make it difficult for products to move and protect the integrity of the product even during hard motion.
2. The blister packaging is beautifully made and has the aesthetic effect of packaging. In our life, some valuable products or gifts need to be put in blister packaging, which can not only increase the beauty of the product packaging, but also make the quality and grade of the product reach a higher level.
3. Blister packaging is anti-corrosion, durable and recyclable. The same product can be recycled in time using blister packaging, which can help us save a lot of packaging costs. It is suitable for a wide range of products, electronics, food, machinery and other components. Blister packaging can be used, and blister packaging is not easy to damage, which is why it is popular. one.
Which material is used for blister packaging?
The sheet used for blister packaging is called rigid sheet or film, commonly used are: PET (polyethylene terephthalate alcohol) rigid sheet, PVC (polyvinyl chloride) rigid sheet, PS (polystyrene) rigid sheet.
1. PS sheet has low density, poor toughness, easy to burn, and produces styrene gas (a harmful gas) when burning, so it is generally used to produce various industrial plastic trays.
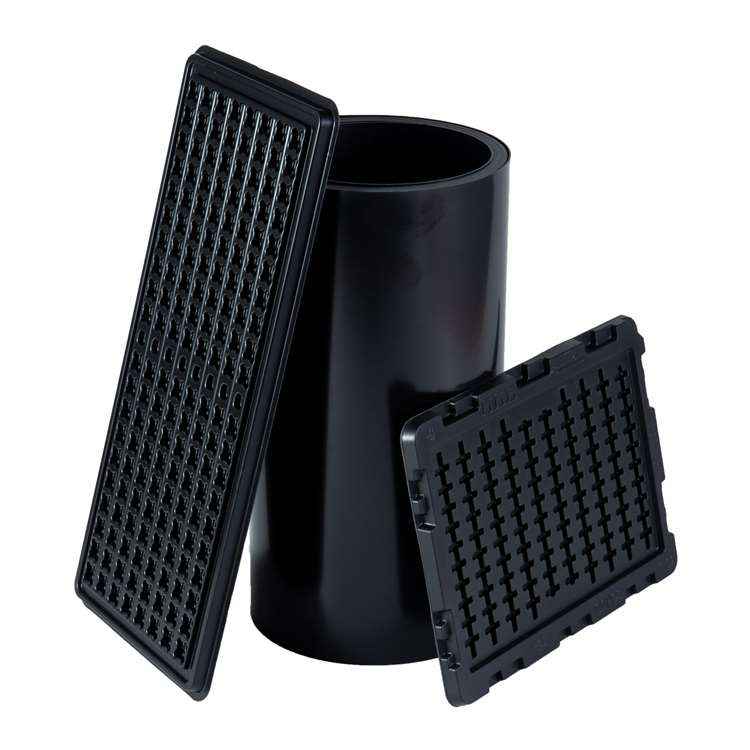
2. PVC sheet has moderate toughness and is not easy to burn. When burning, chlorine gas will be generated, which will have a certain impact on the environment. PVC is easy to heat and seal, and can be sealed by sealing machine and high-frequency machine. It is the main raw material for the production of transparent plastic products.
3. PET sheet has good toughness, high transparency, easy to burn, no harmful gas is generated when burning, and it is an environmentally friendly material. But the price is high, suitable for high-end plastic products. The blister shells of European and American countries generally require the use of PET hard sheets, but it is not easy to heat seal, which brings great difficulties to packaging.
In order to solve this problem, people use a material called PETG (ethylene glycol modified-polyethylene terephthalate), which has both the heat-sealability of PVC and the high environmental protection and transparency of PET. , but the price is higher.
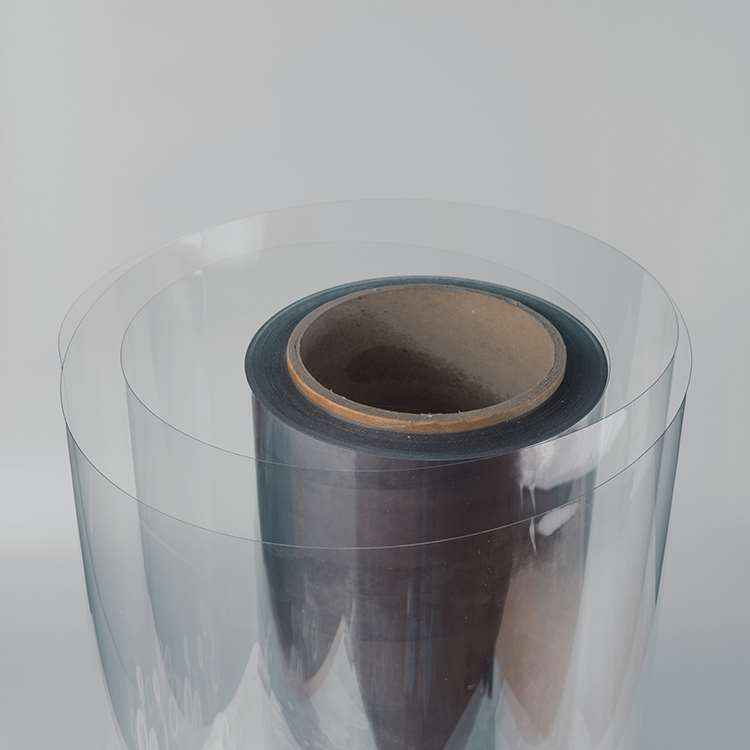
How to open the mold for blister packaging:
1. Plaster mold
Use plaster to carve and shape in a semi-wet state, and then dry it to form a mold. The cost of plaster mold is low, and the general price is about 500 yuan. If the custom-made quantity is small, the plaster mold is generally used, which has the lowest price among the three molds, and the cost performance is also high. And easy to modify, but the plaster mold is not accurate enough, the surface is not smooth and fragile and not durable. Therefore, it is often used for feinting, as a mold for electroplating copper molds or for some plastic molds that are not required to be produced in small batches.
2. Electroplating copper mold
Generally, after the sample is made of plaster mold, a layer of copper shell is electroplated, which is an electroplated copper mold. The cost is higher than that of plaster mold, but it is much cheaper than aluminum mold, and the price is generally around 600 yuan. After electroplating, the mold is more durable and reusable. If you order a large quantity, it is recommended to use an electroplated copper mold, which can save you a lot of cost. Due to the advantages of smooth, durable and low-cost surfaces, electroplated copper molds are the most commonly used blister molds.
3. Aluminum mold
Machined from aluminum ingots (lathes, milling machines, CNC, etc.). Aluminum molds are highly accurate, smooth and durable, but are very expensive. Aluminum molds are generally used on blister products that require higher precision than copper molds.